Cold profiles and roll forming
Cold-formed profiles are thin-walled profiles made from strip or sheet metal that are produced by cold forming - rolling, bending or pressing processes
Due to its high output, roll forming is the most important manufacturing process for cold profiles in industrial production.
Advantages of cold profiles
- Free design of cross-sections to meet functional and structural requirements
- Variety of surface treatments, e.g. pre-coated
- Integration of perforating and perforating operations and profile production into the rolling process
- Tight tolerances
- Good ratio of load capacity to weight
- easy handling
- simple connection
- low processing sensitivity
- low workshop costs
The procedure
Roll forming is a continuous bending process with a rotating tool movement. In this process, the cross-section of a flat sheet metal strip is formed progressively, i.e. in several stages, with the aid of driven pairs of profiled rollers arranged one behind the other on roll stands. As the sheet thickness usually remains constant, this is not rolling or milling in the true sense of the word.
The number of roller pairs depends on the cross-sectional shape to be produced, the material and the specific quality requirements for the profile. Coated or uncoated steel strip or non-ferrous metal strip in the form of coils is the preferred starting material. Although roll forming has been known for over 100 years and has been used industrially since the early 1930s, the process only became established for the production of cold-rolled profiles after the war.
Other terms used for the process of roll forming are:
Roll forming, roll profiling, cold profiling, profiling.
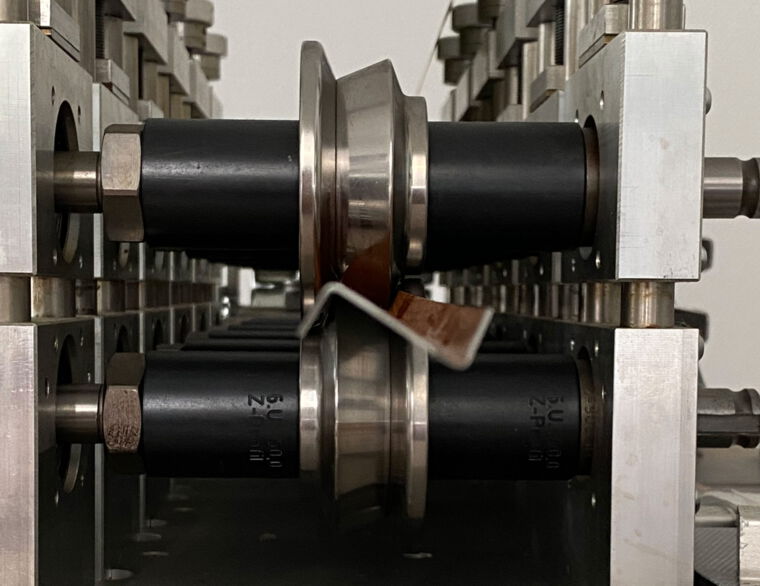
Profile shapes
A distinction is made between special profiles (customer-specific) and standard profiles, as well as between open and closed, symmetrical and asymmetrical and straight and oblique-angled profiles.
Special profiles
In the case of special profiles, the manufacturer produces a cold-rolled profile according to the customer's specifications. The profile manufacturer requires a special roller set for this profile. HUSSMANN PROFILROLLEN can manufacture these roll form tooling.
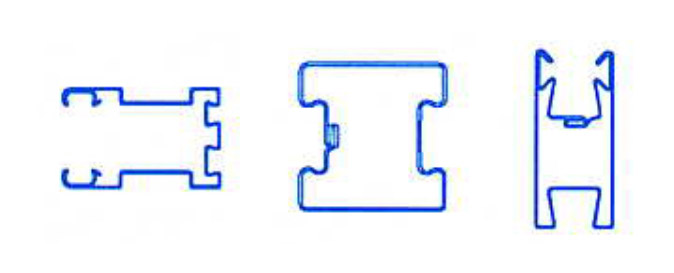
Customer industries for cold profiles
Every manufacturer of cold-formed profiles also offers a certain range of standard profiles, e.g. angle, U, Z, C profiles or slotted tubes.

Dimensions
The maximum possible length of rolled profiles is unlimited in terms of production and only depends on the transportation options. The need for profiles longer than 15 m is not uncommon.
The greatest profile height is the dimension perpendicular to the forming roll axis. It results from the forming conditions and the forming roll diameters and is not necessarily identical to the maximum usable height of the profile.
Advantages of cold profiles
- Construction industry
(interior design, building accessories, noise protection, steel construction, transportation equipment, storage facilities) - Vehicle construction
(road vehicles, wagon construction, shipbuilding) - Electrical industry
(cable ducts, switch cabinet housings, electrical rails, support structures for solar systems) - Mechanical engineering
(conveyor systems, protective enclosures, frames and racks) - Furniture industry
(runners, drawer runners, shelving systems, door frames and profiles)
Tool design
The tool design of a complete roll forming set is based almost exclusively on the experience of the designers and employees in the roll forming companies. However, to support the designer and speed up routine activities, design systems specially developed for roll forming, such as “COPRA” from data M, are now available. However, even these modern CAE systems cannot fully compensate for employee knowledge and accumulated experience, as a large number of complex variables affect the process.
Thanks to intensive research into the fundamentals of the process and the further development of computer technology, the forming process can now be simulated using appropriate analysis tools. This simulation includes the predetermination of the expected profile quality including stresses and changes in shape under specific forming conditions and sheet properties. However, the decisive quality characteristics of rolled profiles are, in addition to dimensional accuracy, low residual macro stresses and low geometric deviations. The Institute of Production Engineering and Forming Machines (PtU) at TU Darmstadt has been conducting research into the fundamentals of roll forming since the early 1980s to provide a broad knowledge base.
Shape deviations
- Torsion
- Longitudinal curvature
- Waviness of the belt edges
Cross form deflections
- Transverse curvature
- Profile end deformation
- Angular deviation
The transverse form deviations as a result of the transverse form changes are a largely solved problem in profiling practice. The control of longitudinal form deviations proves to be much more difficult. They are mainly caused by the longitudinal deformation that occurs in the forming zone and the size of the permanent longitudinal deformation. However, the occurrence of maximum strains and stresses is not necessarily limited to the strip edges. Nowadays, such deviations can already be detected after the design stage with appropriate analysis tools in the simulation phase of the forming process.
Setting up and equipping
The high set-up and adjustment costs of the roll sets counteract the cost-effectiveness of the process. The setting times after a tool change - as well as the design of the roll sets - depend on the experience of the roll forming employees. Until a profile leaves the system in the desired quality for the first time, extensive adjustment work is required on the system, especially during the run-in. It may even be necessary to make design changes to the tools.
At this point, a comprehensive simulation based on the finite element method (e.g. with COPRA FEA RF) pays off, as weak points in the tool design are identified even before the first roll has been produced. This drastically reduces the effort involved in running in a new profile and tryout of the roll set.
Literature
- Comité International du Profilage à Froid, Kaltprofile, Rotterdam 1992
- G. Broer, R. Martin-Bullmann, Kaltprofile, 4. Auflage, Verlag Stahleisen, Düsseldorf 1993
- D. Schmoeckel, K. Damm, Entwicklung und Erprobung einer Meßmethodik zur Kennwertermittlung beim Walzprofilieren für ein CAD-System, Projekt 150, Studiengesellschaft für Anwendungstechnik von Eisen und Stahl e.V., Düsseldorf 1989
- D. Schmoeckel, D. Busse, Eigenspannungsabbau in walzprofilierten Kaltprofilen durch Schwingungsüberlagerung während des Profilierens, Projekt 151 Studiengesellschaft für Anwendungstechnik von Eisen und Stahl e.V., Düsseldorf 1989
- D. Schmoeckel, D. Bussen, Weiterführende Untersuchungen zum Eigenspannungsabbau in walzprofilierten Kaltprofilen durch Überlagerung niederfrequenter Schwingungen hoher Amplitude während des Profilierens, Projekt 209, Studiengesellschaft Stahlanwendung e.V., Düsseldorf 1992
- D. Schmoeckel, N. Stricker, Weiterentwicklung einer Meßmethodik zur Ermittlung technologischer Kennwerte für ein CAD-System durch Formänderungsanalyse in den Einformzonenflächen walzprofilierter Kaltprofile, Projekt 216, Studiengesellschaft Stahlanwendung e.V., Düsseldorf 1993
- D. Schmoeckel, B. Sitzmann, N. Stricker, Entwicklung und Erprobung eines Prozeßsimulationsmodells zur verfahrensspezifischen CAD-Stufenfolgeplanung beim Walzprofilieren, Projekt 219, Studiengesellschaft Stahlanwendung e.V., Düsseldorf 1996
- W. Petzold, H. Launitz, M. Grabe, Ermittlung der Biegewinkelfolge beim Profilieren mit elementaren Berechnungsansätzen, Projekt 225, Studiengesellschaft Stahlanwendung e.V., Düsseldorf 1994
- R. Schwarzwälder, A. Schulte, O. Hahn, J. R. Kurzok, A. Schulte, Entwicklung und Erprobung eines kaltprofilierten Karosseriestrukturteils aus Stahl mit integrierten Funktionselementen für die Großserie, Projekt 331, Studiengesellschaft Stahlanwendung e.V., Düsseldorf 1997
- Kolloquium Walzprofilieren von Stahl, 2. September 1998, Düsseldorf, Tagungsband 722, Studiengesellschaft Stahlanwendung e.V., Düsseldorf 1999
- data M GmbH, Referenzhandbuch, Taufkirchen 1998